Pump Selection Criteria
Pump:
Pump is a most commonly used device in the industry to transfer, raise fluid (liquid or gas) from one location to another by expanding energy. The transfer of fluid can take place with three different modes as volumetric displacement, addition of kinetic energy and the use of electromagnetic force. Generally, pumps are classified in two types: dynamic pumps and positive displacement pumps. For eg. Dynamic pumps as centrifugal and positive displacement pumps as rotary and reciprocating pumps.
Aricle written By : Pallavi Wankhede
On the other hand, there are a variety of designs available for pump in the market. Depending on the industrial application, the pump design must be chosen. The most commonly used pumps for industrial applications are ANSI Centrifugal, Lobe/Sanitary, Self-Priming Centrifugal, Rotary Gear, Horizontal Split Case, Metering/Dosing, Reciprocating Plunger/Piston, Air Operated, High Pressure, Progressing Cavity, Submersible, Vertical Pumps, High Pressure Diaphragm, Magnetically Driven, Multistage pump and the list go on.

Pump Selection:
Selection of pump is primarily based on design, location, space availability, maintenance requirements, reliability, and hydraulic requirements.
Parameter | Centrifugal Pump | Reciprocating Pump |
Optimum Flow and Pressure Applications | Medium/High Capacity, Low/Medium Pressure | Low Capacity, High Pressure |
Minimum Flow Rate | 100,000+ GPM | 10,000+ GPM |
Low Flowrate Capability | No | Yes |
Maximum Pressure | 6000+ psi | 100,000+ psi |
Requires Relief Valve | No | Yes |
Smooth or Pulsating Flow | Smooth | Pulsating |
Variable or Constant Flow | Variable | Constant |
Self-priming | No | Yes |
Space Considerations | Requires Less Space | Requires More Space |
Costs | Lower Initial, Lower Maintenance, Higher Power | Higher Initial, Higher Maintenance, Lower Power |
Fluid Handling | Suitable for a wide range including clean, clear, non-abrasive fluids to abrasive fluids, high-solid content. Not suitable for high viscosity fluids. Lower tolerance for entrained gases. | Suitable for clean, clear, non-abrasive fluids. Specially fitted pumps suitable for abrasive-slurry service. Suitable for high viscosity fluids. Higher Tolerance for entrained gases. |
Pump Location and Space Availability: It includes equipment room or plenum (HVAC guidelines) and elevation.
Reliability: The Study of Pump reliability will give a broad view of how the pump is designed, how the pump is manufactured and assembled, how it is installed, how the product is being pumped, the operating condition for pump, what are the monitoring and maintenance practices for pump. To improve pump reliability in all such aspects is the most technical challenge for the manufacturer and users of pump.
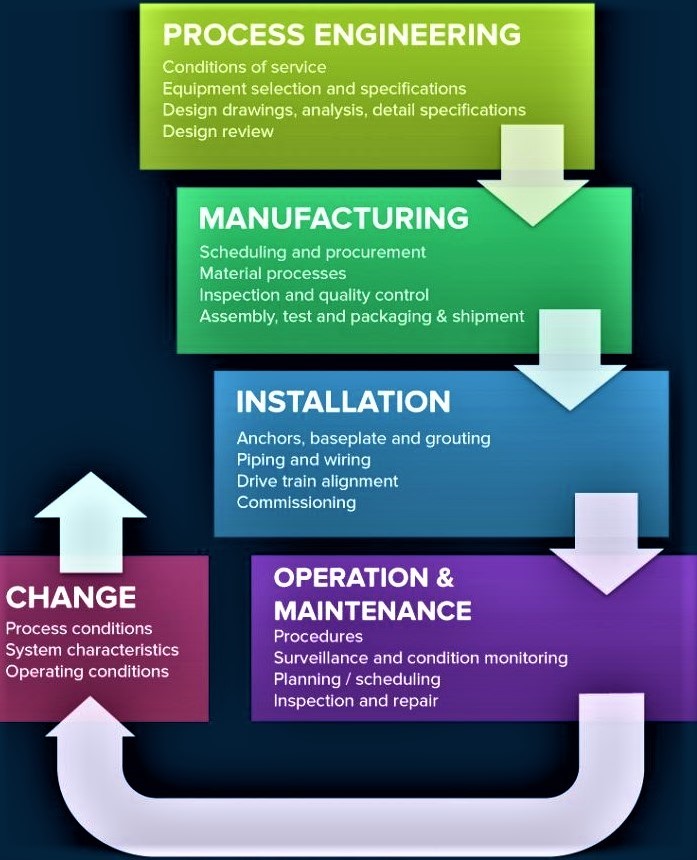
Hydraulic Requirements: It is the most important part of the pump when it comes to selection and designing as well. It includes flow rate, head, efficiency, duty point with respect to BEP (Best Efficiency Point), horsepower and NPSH (Required).

The following Steps must be done while selecting Centrifugal Pump.
Figure 5 : Variation in NPSHR and NPSHA with Discharge Flow
Figure 6: NPSH with respect to Pressure and Vapour Pressure
Pump Efficiency Calculation:
Power Absorbed by Pump Calculation (horsepower):

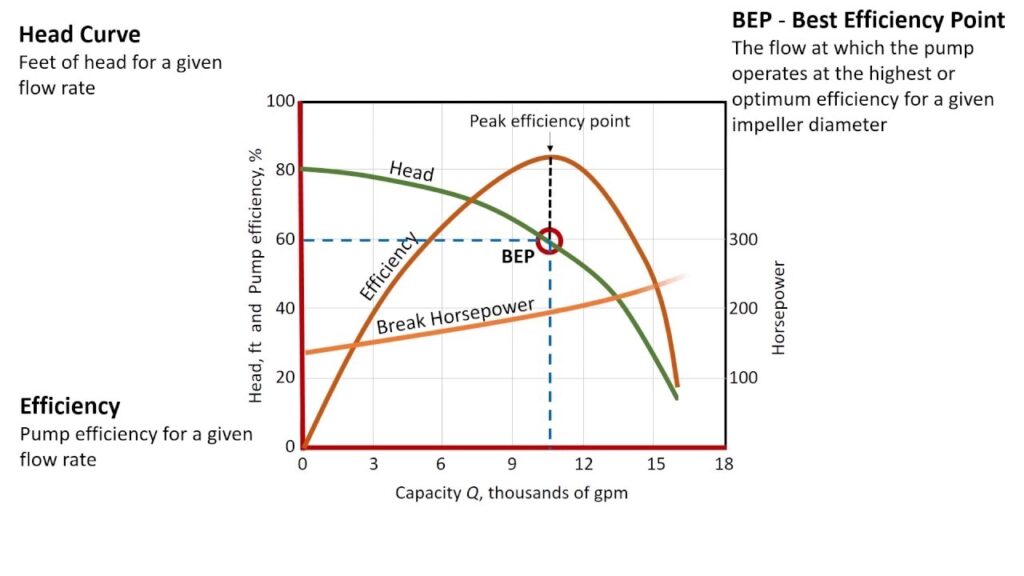
3. Estimate Life Cycle Costs: Pump Initial Cost and its Annual Operating Cost.
Figure 8: Pump Life Cycle Cost
Content Source:
http://www.pumpengineering.net/ ; https://www.britannica.com/ ; https://www.globalspec.com/;
Image Source:
https://empoweringpumps.com/ ; https://www.michael-smith-engineers.co.uk/